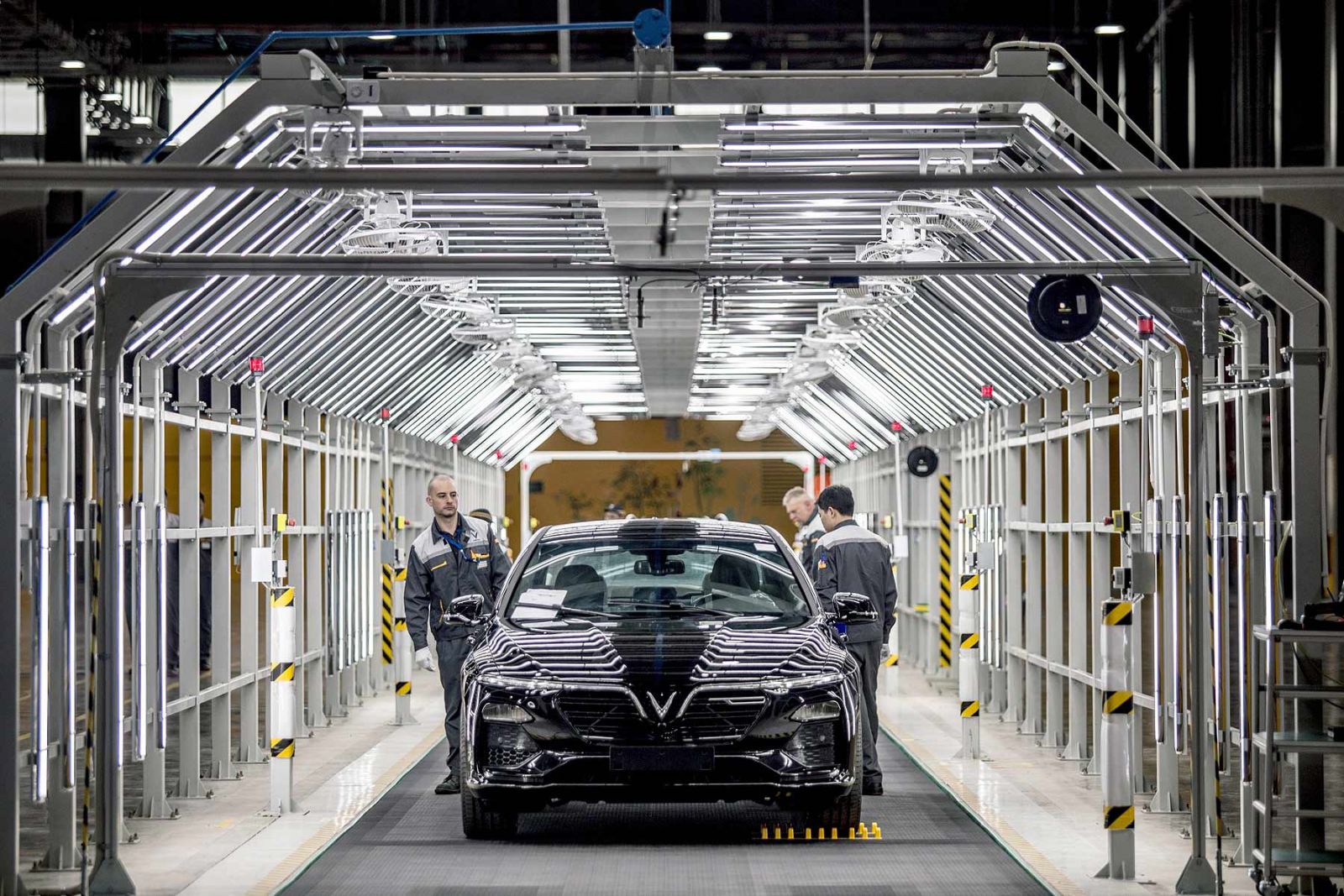
The launch of VinFast automobile factory has signaled an acceleration phase of Vietnam's industrial market.
The Vietnam automobile industry itself contains a great potential. Relentless demand seems to be difficult to satisfy by both domestic and foreign suppliers.
A ninety-four-million-people market along with rising income level is very attractive. The scale of Vietnamese population has gone up steadily from 77.6 million people in 2000 to 93.7 million people in 2017 (growth rate at average 1.13% per year), CBRE reported.
A more impressive trend is that GDP per capita of Vietnam has increased 6 times since 2000. Economic boom has shot the civils’ income up to US$2,385/person in 2017, from only US$404/person in 2000.
Consequently, there is more room in wallet of Vietnamese people for spending on upgrading their personal transportation vehicle. Even though Vietnamese consumers are paying many relevant fees and taxes which make automobile price in Vietnam as three times higher than that of other countries, they are still willing to pay more.
Total automobile unit sale in Vietnam shows an upward trend since 2014. VAMA’s data of July 2018 recorded 21,466 units absorbed by the market, which increase 3.89% y-o-y. Sale growth rate of market reached 23% on average per annum from 2014 to 2017.
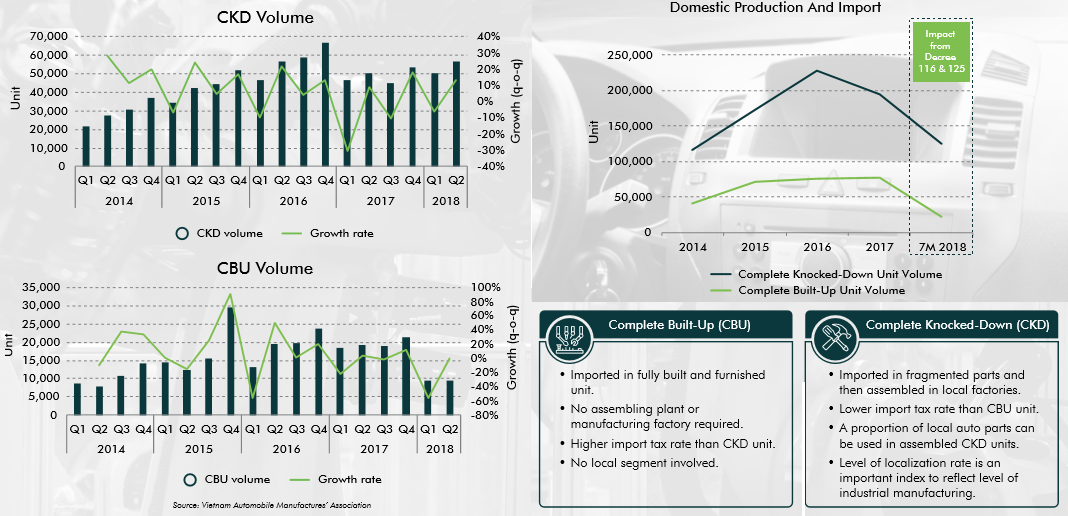
In terms of production, Complete Knocked-Down car (CKD) volume has gone up sharply. Total 228,476 vehicles assembled in Vietnam as of 2016, showing an increase of 32% y-o-y.
Import volume of Complete Built-Up car volume (CBU) fluctuated even more wildly in comparison with CKD. It reached the peak of 12,577 CBUs in November 2015 before dropping to 2,475 units in February 2016. The aim of government to control CBU volume has imposed significant influence on the CBU segment and made it more unstable.
Obviously, either CKD or CBU segment developments revealed that Vietnam is so far growing with a very fast pace.
Huge potential of growing automobile market attracts more and more foreign investors regarding assembling, trading as well as accessories manufacturing. Auto part manufacturers, following the expansion wave of domestic car assembling, also take actions to join the market or at least enhance their presence.
In fact, the reported FDI figures have released optimistic signals for the industry. From 2014 to 2017, both registered FDI capital and number of FDI projects increased steadily, of which manufacturing accounts for 52.44% of total projects and 57.72% of total registered capital on average.
Automobile trade and repairs, meanwhile, only accounts for nearly 9.42% of total projects as well as 1.75% of capital. However, this sector recorded a very impressive growth rate at 15.45% y-o-y in terms of number of project.
Furthermore, foreign capital flow into automobile retail trade and repair sector has grown by 26.60% y-o-y since 2014, which is a firm evidence for increasing interest of foreign investors on Vietnam automobile industry.
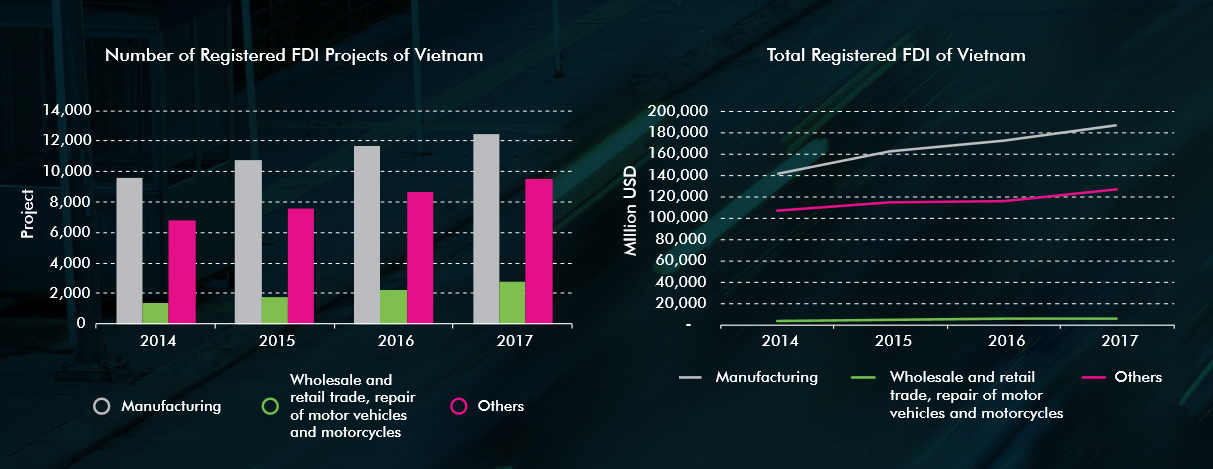
(Source: CBRE)
In comparison with Thailand and Indonesia automobile industry, Vietnam’s one is much weaker in terms of production scale as well as capability. The main reason why the neighbor industries gain so much more achievements is the important role of protection policies of governments for their domestic industry.
One of the most difficult challenges of Vietnam automobile industry is its low localization rate. It could be observed that the main purpose of government’s domestic industry protection is increasing localization rate which is now only at 23%. Even though the outlook of Vietnam automobile market is optimistic, and the potential is huge, but the current market size is insufficient, of which domestic demand is not enough to ensure economies of scale.
Fourteen original equipment manufacturers (OEMs) are operating in Vietnam in both CKD assembling as well as CBU importing. Their expected number of cars sold is much more than 270,000 units on average per year as reported now. Furthermore, there are OEMs which consider closing their Vietnamese plants and shift to importing from regional production hubs, especially Thailand, due to the removal of tariffs from ASEAN countries.
Besides, automakers not only need to build factories and warehouses but also prepare customized equipment to produce 4-wheel cars, which might be considered as risky investments for producers who have low capital. Labor wage’s growth rate of Vietnam is faster than that of productivity growth and this also make Vietnamese car production cost higher.
Ford has publicly stated that the cost of local production was 20% higher than CBU imports.
Accordingly, Vietnam’s manufacturing cost is about 5-10% higher than Thailand due to auto parts are imported instead of purchasing from local market, which makes costs higher due to import tax, transportation & packaging costs. In competition with foreign auto part makers, Vietnamese rivals are also weaker in terms of technological capability.
Lack of manufacturing experience, low safe code and quality assurance as well as small production scale are main reasons why Vietnamese auto part makers themselves are being overwhelmed in their own playground.